螺紋刀片選用
為了使您有良好的加工品質,在選購和使用時請考慮以下幾點:
1、根據加工內、外螺紋、螺紋旋向及工件螺距、牙數(shù)/英吋,按我們提供的“切削外(內)螺紋用刀片”表選擇 合適型號的螺紋刀片(樣本),并請與我們的銷售人員商量,根據被加工零件的材料,選擇最適合您使用的刀片牌號。
2、根據您所采用的車床的型號,加工方式及已選用的刀片型號來選擇適當?shù)牡稐U型號。
3、刀墊選擇:螺紋的螺旋升角必須和刀片的傾斜角一致,盡可能避免后刀面一側的不利磨損,致使刀具壽短。我們在制造螺紋刀桿時已經將刃傾角(λ)值設計為1°
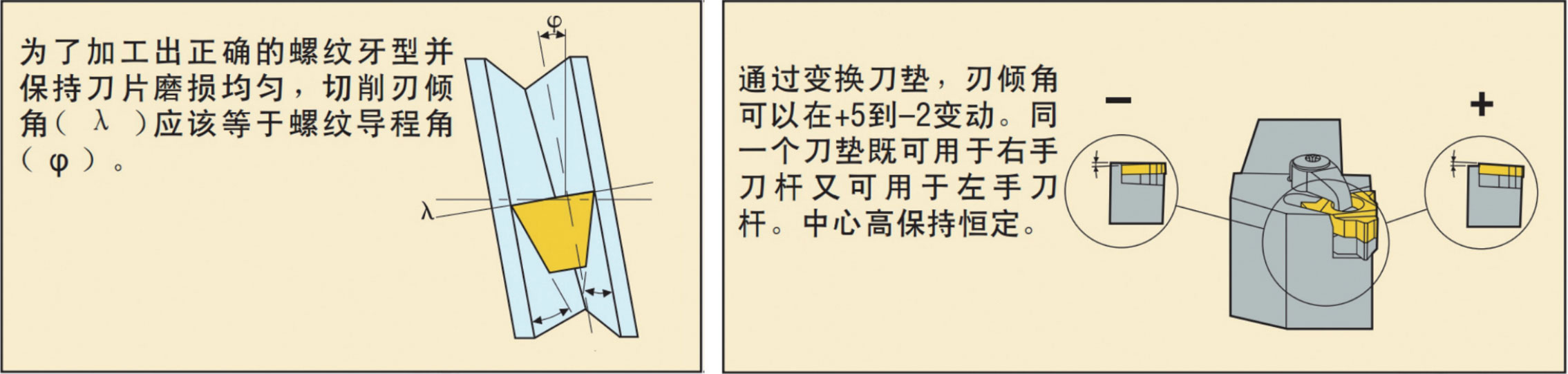
?4、切削速度的選擇:
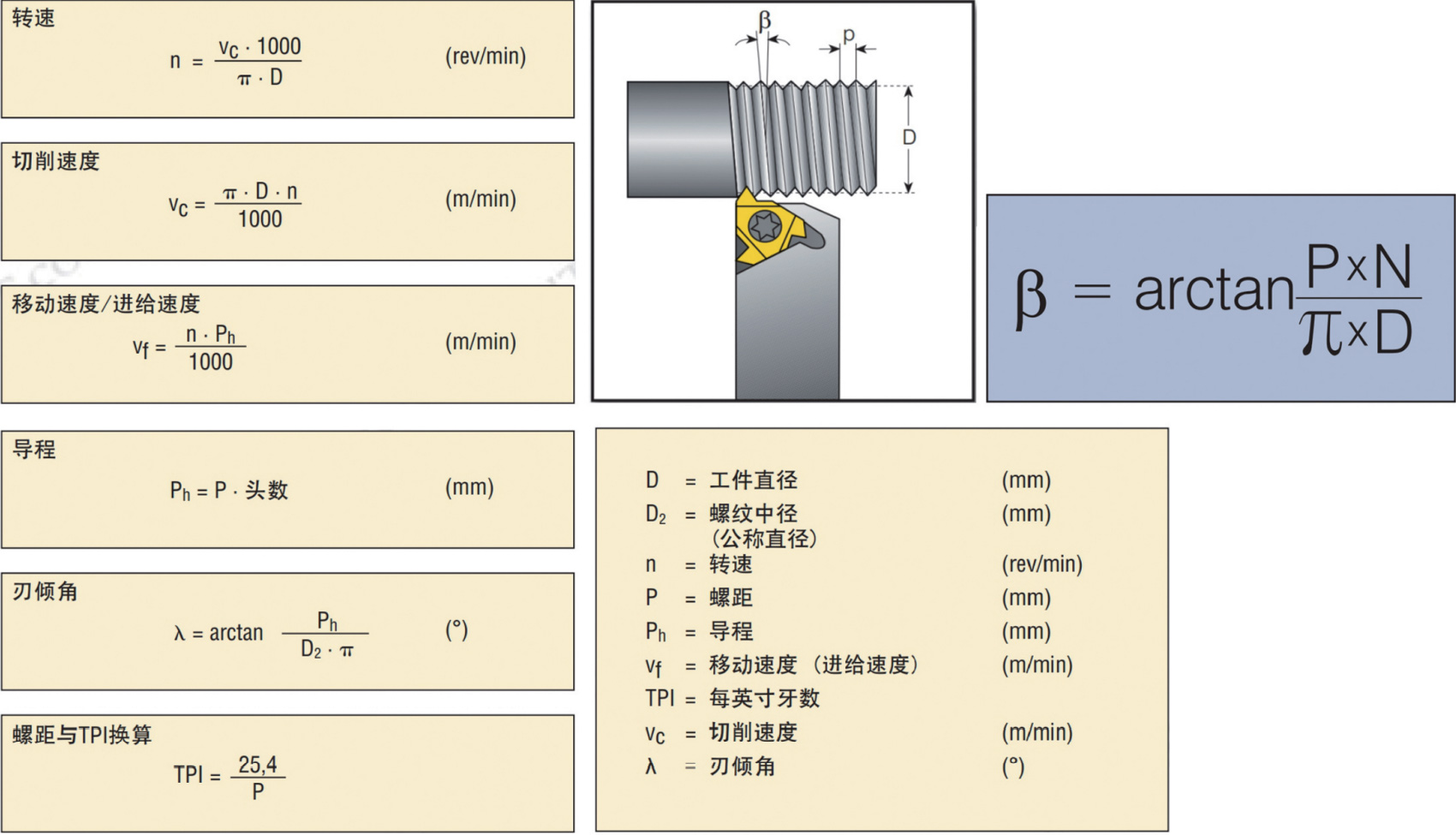
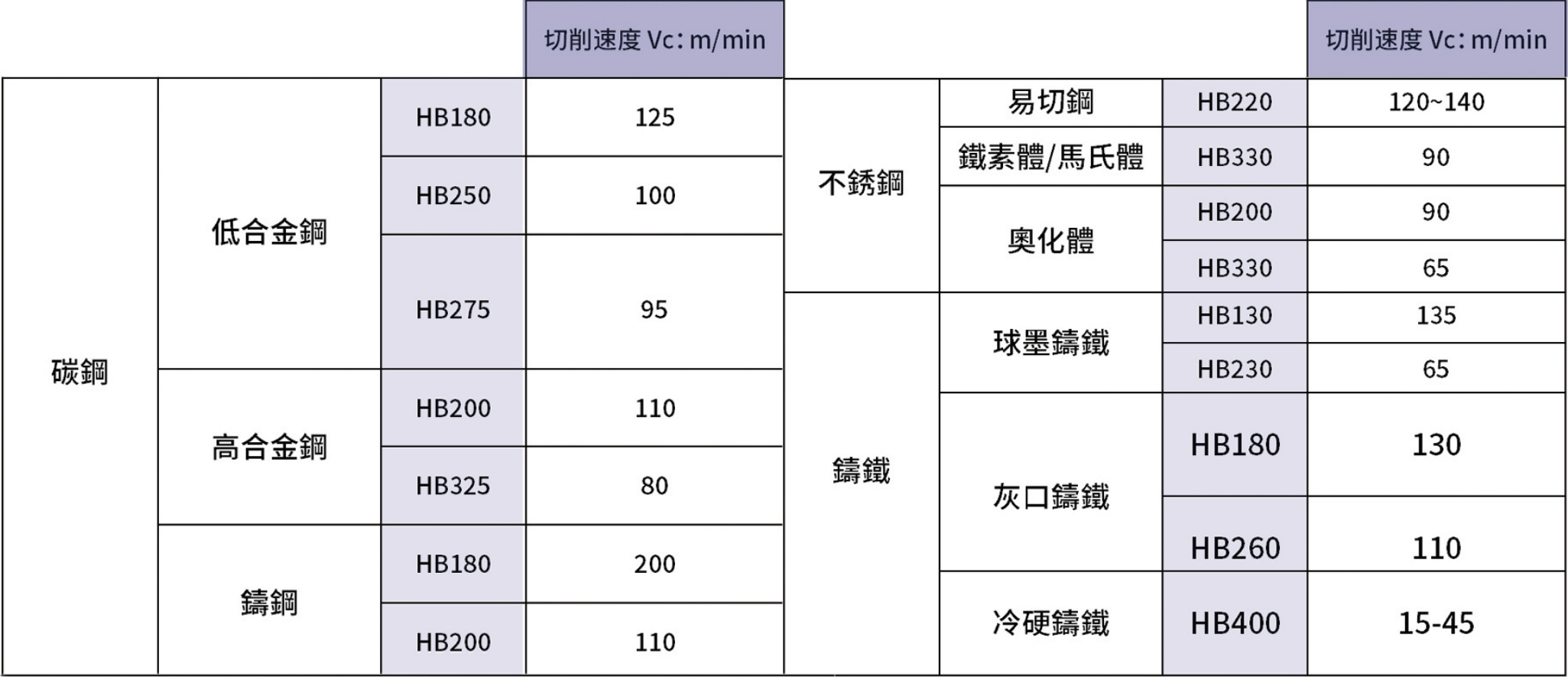
對于不銹鋼的螺紋切削,最重要的是切削速度VC要足夠高,以避免“積屑瘤”現(xiàn)象。
為了提高小刀尖角刀片的壽命,比如NPT螺紋,可先用較大刀尖角刀片先加工一次,或將切削參數(shù)相應改變(增加切削次數(shù))。
5、進刀方式選擇
- 徑向進刀:通常車削螺紋時,應先選擇徑向進刀的方式進行,此法操作筒單,且對有加工硬化傾向材料如 奧氏體不銹鋼材料的首選。當加工大螺距時,易產生振動,可改為側向進刀法或互動式進刀方法。
- 側向進刀法:易于對切屑流向的控制,便于切屑的排出及減輕車削螺紋時的振動,螺紋的表面粗糙度良好。為了在側向進刀時保持刀片齒形仍能獲得均勻的磨損,對600公制螺紋采用在徑向切深AP的同時,在軸向進給 1/2 AP的方法獲得:
- 互動式進刀:大螺距粗牙螺紋首選,可明顯減少刀片磨損,提高刀具壽命,易產生斷屑問題,適合CNC數(shù) 控機床上使用。
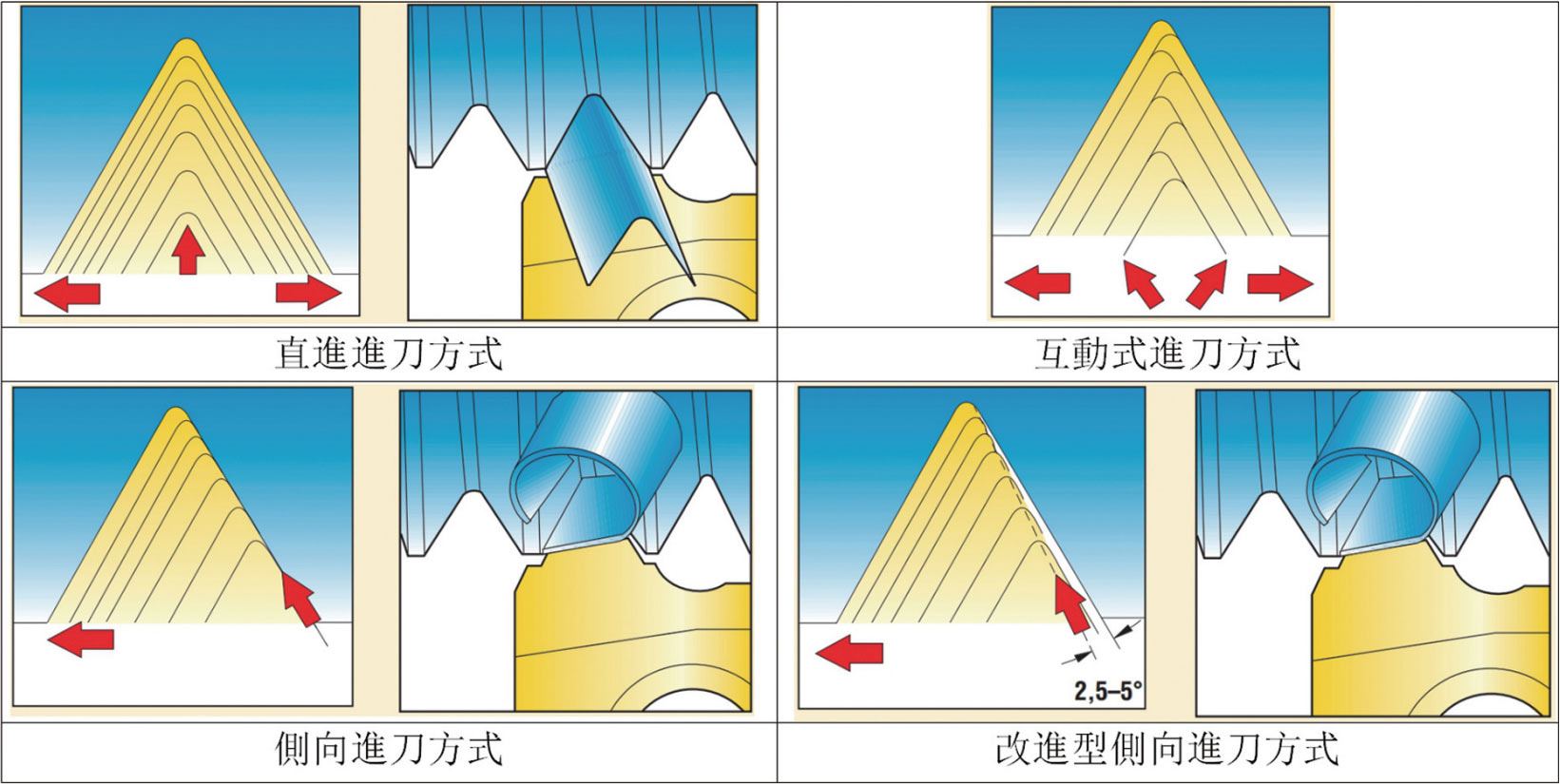
6、步數(shù)與進刀深度
由于相對較脆的切削刃,螺紋不能一次切削完成。總的切削深度要分幾步完成,每一步都需保持相近的切削力 (相同的切削面積)。
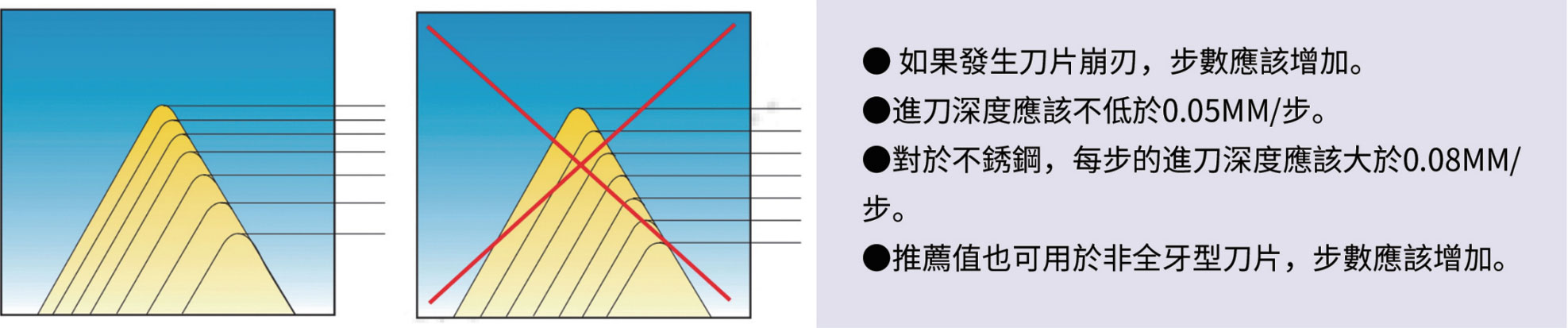
7、進刀量推薦值
在大多數(shù)CNC機床上,螺紋加工的一個周期中,(如螺紋加工的固定回圈)總的螺紋深度和第一刀或最后一 刀的切深AP值應給出而在第一次進刀時采用最大的進刀深度(刀尖圓弧半徑的1.5?2倍),隨后的進刀深度應逐 漸減小。最后一刀的進刀深度應不小于0.05MM的單邊進刀量,否則易造成刀尖的磨損和工件齒面光潔度較差。
在目前的數(shù)控機床中,螺紋切削(固定回圈)有兩種加工方法:
- 徑向進刀法均采用G32方式;(G33、G34、G35);
- 側向進刀法較多采用G76方式;
由于切削方法不同,編程方法不同,造成的加工誤差不同。
兩種加工方式的編程指令。
(A) G32X (U) ---Z (W) ---F------;
G32編程:切削深度分配方式一般為常量值,雙刃切削,每次的切削深度AP編程人員給出。
徑向進刀法由于雙側刃同時工作,切削刀較大,而且排屑困難。因此在切削時,兩切削刃容易磨損。在切削螺距較大的螺紋時,由于切削深度較大,刀刃磨損較快,從而造成螺紋中徑產生誤差。由于其加工的牙形精度較高,多用于小螺距螺紋加工中,注意一點的是,刃口容易磨損,因此加工中要做到勤測量。
(B) G76P (M) ? (2) Q (ADMIN) R(D);
G76X (U) Z (W) R ( ) Q ( ) F ( );
G76編程:切削深度分配方式為遞減式,其切削為單刃切削,其切削深度由控制系統(tǒng)自動計算給出。
G76側向進刀法,由于為單側刃加工,加工刃容易損壞和磨損,使加工的螺紋表面不直,刀尖角發(fā)生變化, 而造成牙形精度降低。同時其為單刃切削,刀具負載較小,排屑容易,及減輕車削時振動。此種方法一般適用于 大螺距螺紋加工。在加工較高精度螺紋時,建議采用“雙刀”切削,即是先按G76方法時行粗加工,G32方法進行精加工。注意一點的是刀具起始點要準確定位一致,否則易造成亂扣。